What is Water Cutting?
Waterjet, also known as water cutting, scientific name is high-pressure water jet cutting technology. It is a widely used abrasive cutting tool today. It has many advantages such as good cutting quality and no thermal processing, and has been well received by the market. What we are sharing today is the principle, advantages and disadvantages of water cutting.
How water cutting works
In the early water cutting, due to the small water pressure, no abrasive was added, and it could only be used to cut relatively soft and low-strength materials such as paper, which has a very narrow application range.
Later, with the development of technology, high-pressure water pumps can be used to cut more materials. Early water cutting relied entirely on water pressure to cut materials, but only materials with a lower material strength than water pressure could be used. Great limitation.
The water pump pressurizes the water, but the pressure is not enough. What to do? I have to add a booster pump to pressurize the water again to reach the desired pressure. Note that the abrasive cannot be added to the water source or high-pressure water pipeline. , Because the pipeline will be worn through soon, how to add it, can only be added at the nozzle position, let the water and abrasive mix, can not be too close to the exit, because to accelerate him for a distance, only the abrasive has a certain The flow velocity is more lethal, so will the mixed fluid of abrasive and water not wear the nozzle, yes, surely, this is like a seven-injury fist, hurting yourself first and then hurting people, is there any way to avoid it? No, it can only increase its own hardness, so water cutting nozzles are made of very hard and strong materials, such as tungsten carbide ceramic composite materials.
The high-six-speed abrasive passes through the material being cut just like sandpaper. It will grind a little metal without passing through it. The continuous high-speed abrasive water mixture and the metal constantly rub, and the effect of the electric wheel is almost the same.
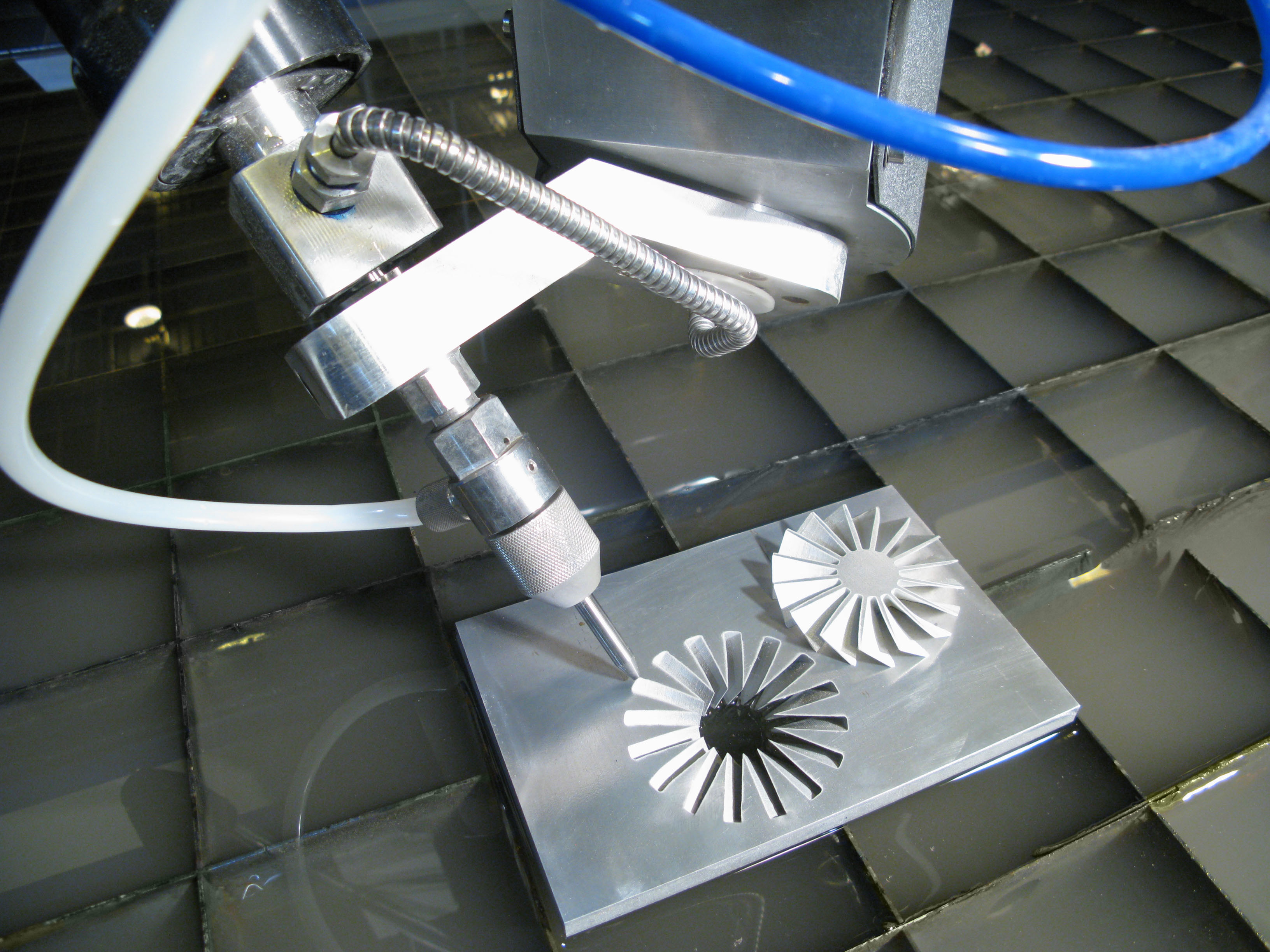
Water cutting advantages
1.Wide range of cutting
Can cut most materials, such as: metal, marble, glass, etc.
2.Good cutting quality
Smooth cuts without rough, burr edges.
3. No thermal processing
Because it uses water and abrasive cutting, it does not generate heat (or generates very little heat) during processing. This effect is ideal for materials affected by heat. Such as: titanium.
4.Environmental protection
This machine uses water and sand to cut. This kind of sand does not generate toxic gas during processing and can be directly discharged, which is more environmentally friendly.
5, no need to change tools
You don't need to change the cutter unit, one nozzle can process different types of materials and shapes, saving cost and time.
With so many advantages, of course, they are widely used now. 3 axis / 4 axis / 5 axis water cutting machines are more common. Water cutting can cut out the whole impeller, which is very powerful!
Disadvantages of water cutting
Disadvantages of water cutting
1. High use cost, requiring a lot of water and sediment;
2. Great pollution to the production environment;
3. High maintenance cost;
4. Cutting carbon steel plate is easy to rust, which affects the aesthetics of the product.
Water cutting thickness
Normal water pressurizes water to 4,000 bar (60,000 psi) through an ultra-high pressure intensifier, and then through a small nozzle (0.004 inches to 0.016 inches in diameter) produces a water arrow speed of 915 meters per second at about three times the speed of sound Water Arrow can do a variety of surface treatments and cut a variety of non-metallic materials such as paper, diapers, glass, optical fibers, sponges, etc.
For cutting metal and hard materials, such as various stone, glass, ceramics, ceramic tiles and other materials, mix garnet in high pressure water to improve their cutting ability. This high-speed sand cutting can cut almost any material. In general, the water cut steel plate test has reached a maximum thickness of 200mm.