How to understand or judge the two types of risk tested with this sampling plan
How to understand or judge the two types of risk tested with this sampling plan
In the sampling inspection, the OC curve can be used to evaluate the discriminative ability of the sampling plan, but how a sampling plan affects the interests of the producers and users can be specifically analyzed through two types of risks.
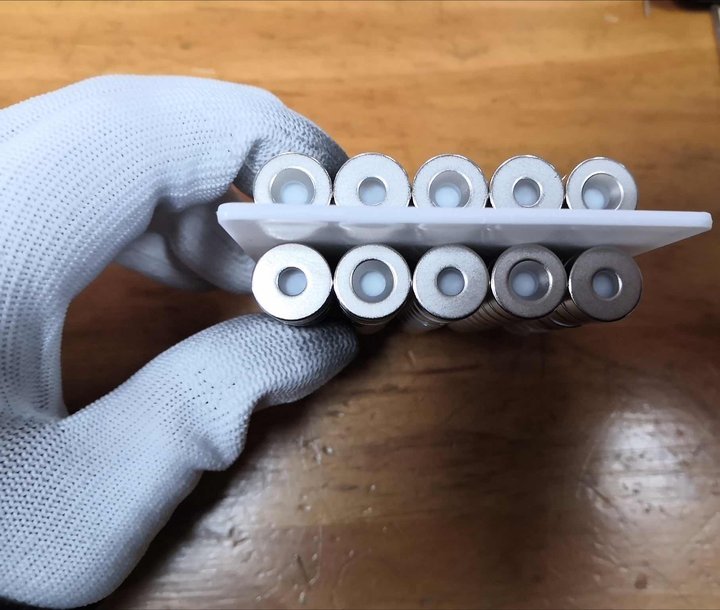
1. Producer Risk
When sampling inspection is adopted, both the manufacturer and the user must take certain risks. Because sampling inspection is to take samples from the batch for inspection according to a certain sampling plan, and judge whether the batch is accepted or not according to the inspection results and the acceptance criteria. Due to the randomness of the sample, and at the same time it is only a part of the batch, usually a small part, it is possible to make a wrong judgment. Originally good quality batches may be judged not to be accepted; originally poor quality batches may be judged to be accepted. The risk of the producer refers to the risk that the quality of the batch undertaken by the producer is not accepted, also known as the probability of the first type of error, generally expressed by α. For example, there is a batch of products, the batch N=1000, the number of unqualified products in the batch D=1, that is, the batch of unqualified products rate is one thousandth, the manufacturer and the user are satisfied with the quality of this batch of products. Suppose a very simple sampling plan is adopted, that is, only one unit of product is sampled for inspection, and if it is a conforming product, the lot is accepted; if it is a non-conforming product, the lot is not accepted. During sampling inspection, two situations may occur: The first case: n=1, d=0, receive the batch of products; The second case: n=1, d=1, this batch of products is not accepted. In the first case of the example, qualified products are drawn, and the batch of products is received according to the inspection plan. This result meets the requirements of the manufacturer and the user; but if the only unqualified product in the batch is just drawn, the inspection result is not. Accept the batch. This is completely detrimental to the producer. With sampling inspection, the producer will have such a risk.
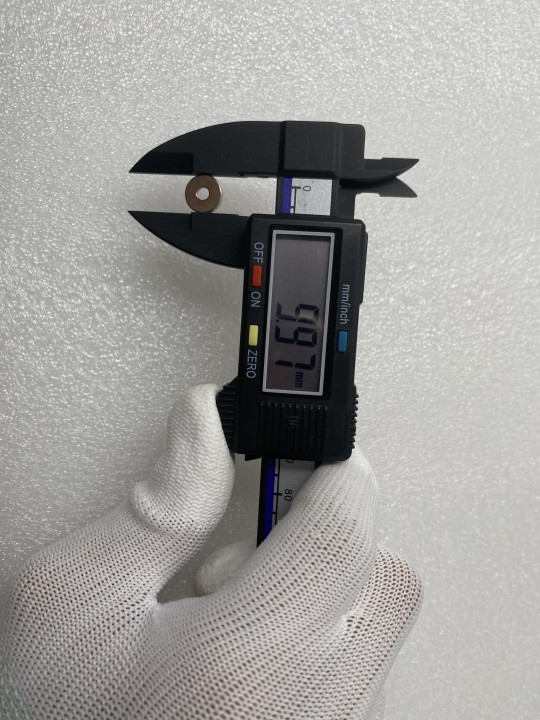
2. User risk
User risk refers to the risk that the user bears to receive batches of unqualified quality, also known as the probability of Type II error, generally expressed by β. For example, there is a batch of products, the batch N=1000, the number of unqualified products in the batch D=500, that is, the batch of unqualified products rate is 50%, this batch of products is of course unqualified. Suppose an insurance sampling plan is adopted: n=500 units of product are sampled for inspection. If there is no non-conforming product in the sample, the batch will be accepted, otherwise it will not be accepted. But even so, according to the sampling plan, it is still possible that all 500 qualified products in the batch will be judged to be accepted. Once this extreme situation occurs, it will of course damage the interests of the user.
It is impossible to happen in practice, but this also shows that as long as sampling is carried out, the user must also have certain risks. The above two types of risks are unavoidable in sampling inspection. To adopt a sampling plan, both the producer and the user must bear their own risks. The key is that both parties should be clear about the limits of risk they are taking. For both parties, what kind of quality level is a qualified batch, and at this quality level, the maximum risk of the producer does not exceed how much; what kind of quality level is an unacceptable batch, under this quality level, how much can the user bear risks of. On this basis, a suitable sampling plan can be found by comparing the acceptance probability and QC curve of the alternatives. If we want to satisfy the interests of both parties and reduce the risks of both parties at the same time, the only way is to increase the sample size, but this will inevitably increase the inspection cost. Therefore, the choice of sampling plan is actually a balance between the risks borne by both parties and the sampling economy.