Surface Treatment of NdFeB Magnets - Phosphating
The PrNd in NdFeB is a metal that is easy to oxidize, and the iron element with the largest content is also a substance that is easy to oxidize and rust. Therefore, a finished product will be usually protected by a coating. The most common coating is zinc plating and nickel plating, compared with these two coatings, passivation and phosphating are relatively rarely used, especially phosphating. This article will focus on introducing the relevant knowledge of phosphating surface treatment of NdFeB magnets.
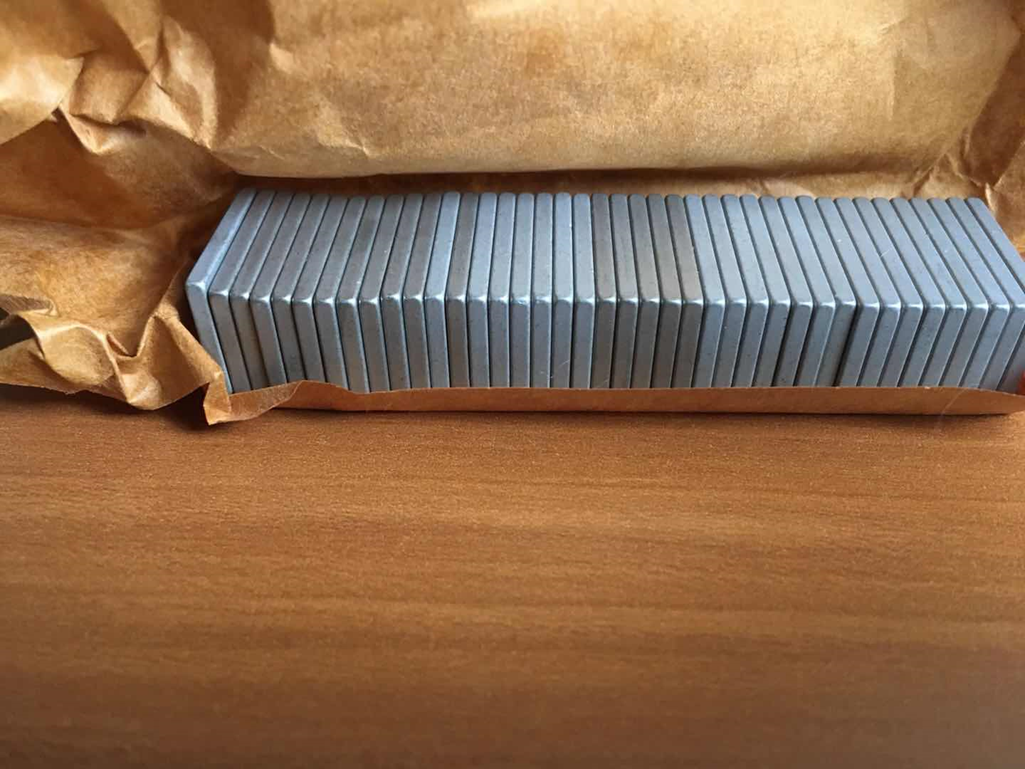
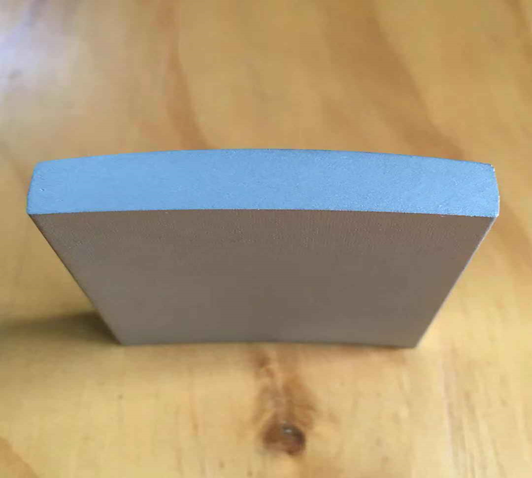
The Purpose of NdFeB Magnets Phosphating
The phosphating surface treatment of sintered NdFeB magnet has two purposes. The first is to prevent corrosion in the process and to improve the bonding strength of the subsequent process. The second is to improve the surface epoxy wettability.
1. Corrosion Resistance
Due to the low density and porous characteristics of the sintered NdFeB surface, the exposed magnet will be oxidized in the air, which is also called corroded. Therefore, it is necessary and effective to use phosphating process for simple anti-corrosion treatment when the NdFeB magnets are too long in turnover and storage time, and when the subsequent surface treatment method is not clear.
The phosphating process is simple and does not require much equipment investment. The phosphating production process consumes less, mainly acid, alkali and phosphating solution. Also, the production cost is low. As a process anti-corrosion, it will not significantly increase the production cost of the magnet, and it can avoid the less of magnets during the storage period and the return rate is very high. After phosphating, the product has a uniform color and a clean surface. It can be vacuum packaged to greatly extend the storage time. The storage method is better than the previous storage methods of oil immersion and oil coating. The complete phosphating film can resist oxidation and corrosion in normal atmospheric environment. The subsequent surface treatment of phosphating magnet products is easy, and the phosphating film can be completely removed by simple pickling. It will not have adverse effects on subsequent surface treatments, such as zinc plating, nickel plating, etc., and the subsequent surface can be completed at any time treatment process.
2. Improved wettability
Some NdFeB magnets need to be bonded by epoxy adhesive or be painted. The bonding force of epoxy organic compounds such as glue and paint requires good wettability of the matrix. Phosphating film and epoxy organic matter have good wettability, so phosphating process is needed to improve the wettability of NdFeB magnet surface. Good wettability can ensure the bonding force of epoxy glue, epoxy paint and magnet.
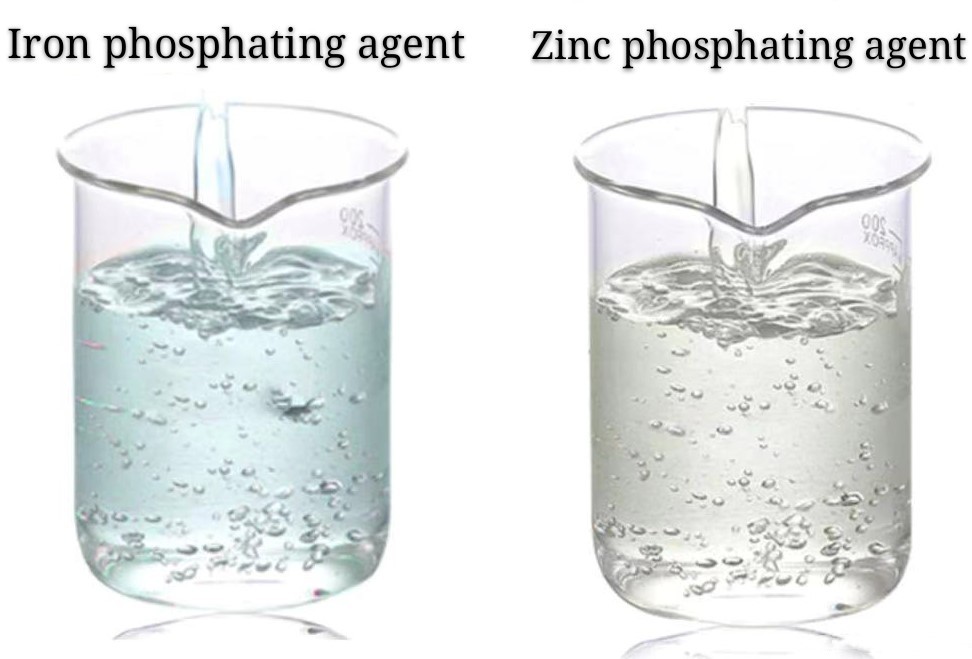
Process Flow of Surface Phosphating of NdFeB Magnets
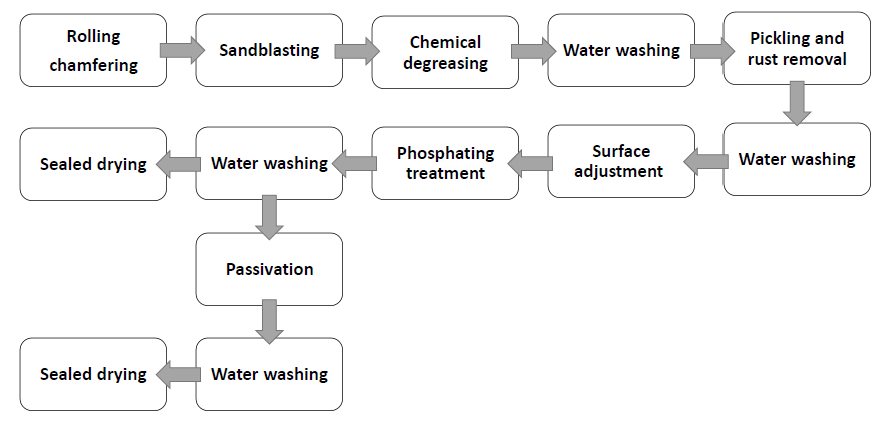
Step1:Rolling chamfering:A vibration grinder is used to place the NdFeB material and abrasive into the grinder for grinding.
Step2:Sandblasting: Sandblasting can remove obvious rust on the surface and avoid strong corrosion in the subsequent process
Step3:Chemical degreasing: Weak alkaline substances are used for degreasing, and anionic surfactants are the main components. Ultrasonic waves can be used to enhance the degreasing effect.
Step4:Water washing
Step5:Pickling and rust removal: Conventional rust removal often causes excessive corrosion of materials, so phosphating uses a method of removing rust by adding corrosion inhibitors.
Step6:Water washing
Step7:Surface adjustment: It is a special surface treatment on the surface of NdFeB magnet to adapt to the formation of phosphating film. The surface adjustment of NdFeB magnets generally adopts weak acid soaking to improve the alloy composition of the magnet surface to achieve the purpose of facilitating the formation of phosphate film. The phosphating process currently mainly uses commercial phosphating solution for production
Step8:Phosphating treatment:Phosphating adopts room temperature zinc phosphating, and the phosphating solution is mainly composed of nickel salt, zinc dihydrogen phosphate, molybdate, fluoride, and complexing agent. Commercial phosphating solution is divided into zinc series, iron series, manganese series, binary, ternary, multi-element and other varieties. Each system has its own advantages and disadvantages. Therefore, in the production and application of NdFeB phosphating, the magnet manufacturers will use their own appropriate supply varieties due to the different purchase price and use effect. Some NdFeB products require phosphating after galvanizing, and then the zinc-based phosphating solution or multi-component phosphating solution which contains zinc will be used to do phosphating after galvanizing.
Step9:Water washing
Step10:Sealed drying
*** Sometimes a passivation treatment will be performed before the sealing and drying treatment. A solution containing hexavalent chromium is used for passivation. Combined with a passivation treatment, it will improve the corrosion resistance of the phosphating film.
The Impact of Temperature to the Phosphating Film
Phosphating process is divided into three types in terms of temperature: high temperature, medium temperature, and normal temperature. Generally, the high temperature process has a thick film layer, and the phosphating film is of great density and thickness; the normal temperature process generally has a thin film layer; the medium temperature process is somewhere in between. Magnetic material manufacturers mostly use normal temperature processes, but normal temperature processes also require temperature control to ensure temperature stability (15°C-35°C).
The Reasons for “Still Rust after Phosphating”
Magnetic material still rusts after phosphating. There are many reasons for this phenomenon. For example, the concentration of phosphating agent in the phosphating pool is not high enough, resulting in the phosphating film being too thin or loose; failure of insulation of air; the water being not clean after phosphating; high concentration of aid in the washing pool, remaining acidic substances on the magnetic material, and causing the acid solution destroys the phosphate film and rust. In addition, whether the degreasing is complete should be checked, as incompletion of degreasing affects the phosphating effectiveness as well. To ensure the phosphating effectiveness, during the phosphating process, special attention should be paid to the distribution ratio of the phosphating solution and appropriate temperature; the phosphating time is controlled at 10-15 minutes. To achieve fully phosphating, hanging or reducing loading can be used to ensure that there is a little gap between magnetic workpieces.
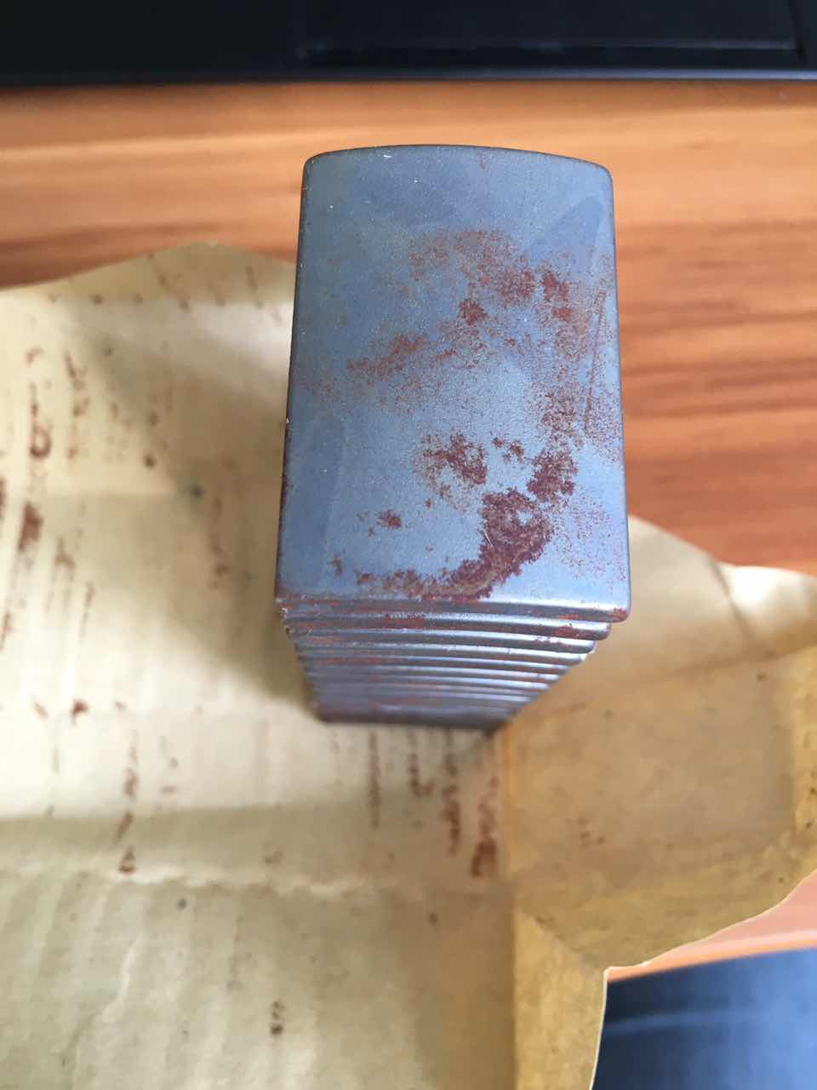
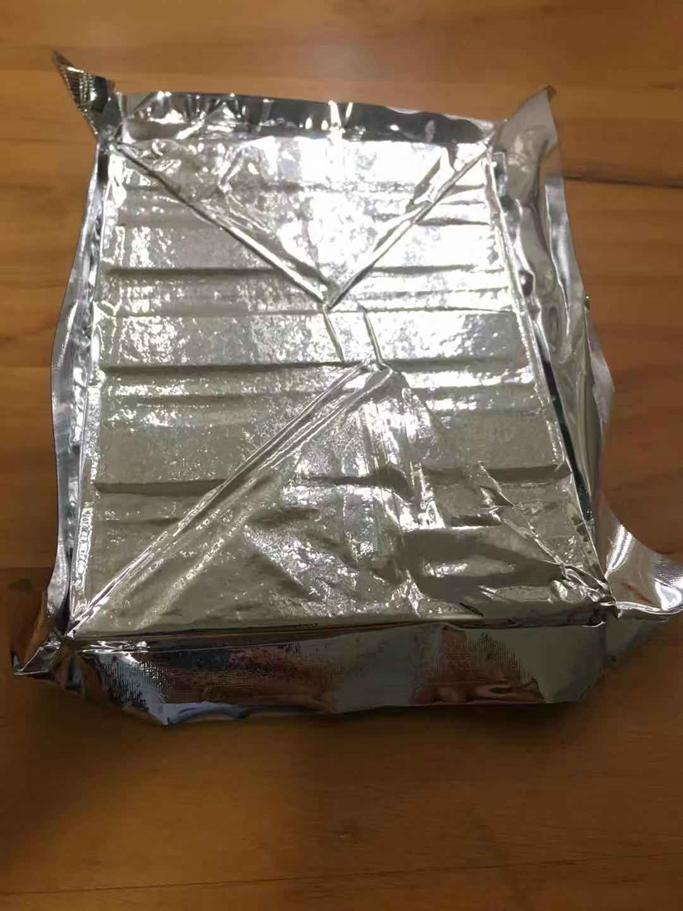
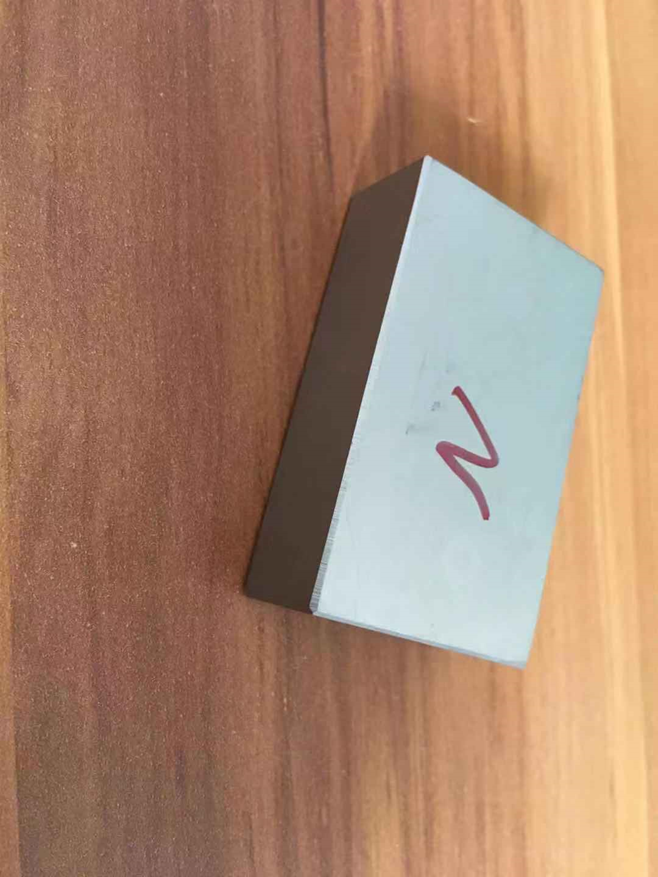
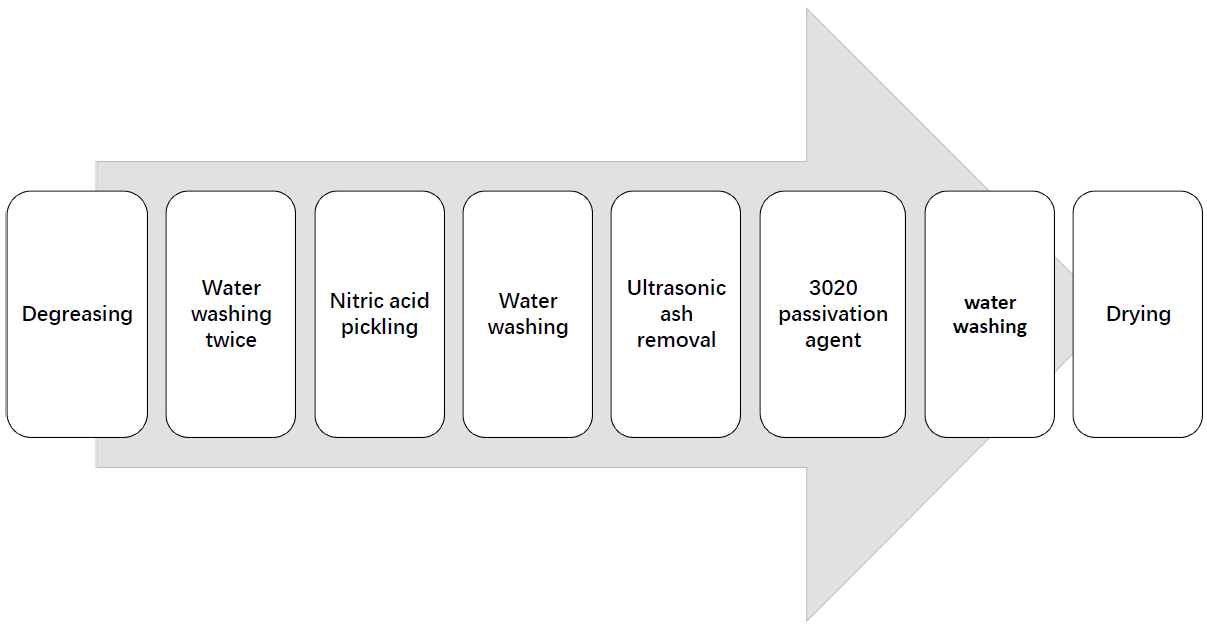
Step1:Degreasing: Both organic cold degreasing or alkaline thermal degreasing are applicable to remove oil stains on the surface of the workpiece (such as machining cutting fluid, anti-rust oil, etc.)
Step2:Water washing.
Step3:Nitric acid pickling: Use 50-60ml/L of 65% nitric acid. Additives can be used appropriately. The recommended processing time is 30-40S to remove the surface oxide layer of the workpiece.
Step4:Water washing.
Step5:Ultrasonic ash removal: Use the high-frequency vibration of ultrasonic waves to remove the floating ash on the surface of the workpiece and the residual acid in the pore.
Step6:Water washing.
Step7:3020 passivation agent: Concentration: 5-10%, pH: 7.5-9, time: 3-8 minutes, temperature: room temperature, a 30-50nm passivation film is formed on the surface of the workpiece.
Step8:Water washing
Step9:Drying: It is recommended to bake after air drying. Baking temperature: 60-80℃, time: 10-20 minutes
Conclusion
NdFeB passivation is similar to phosphating, which is a chemical method applied on NdFeB surface, forming a protective film on the surface of the workpiece as a way to avid corrosion of the workpiece. Surface chemical conversion coating technology is a common method of surface treatment. At present, NdFeB surface chemical conversion coating treatment mainly uses phosphating technology, mostly ordinary zinc or iron phosphating. The phosphating film has poor corrosion resistance and often does not perform the anti-corrosion function itself, but cooperates with electrophoresis, coating, etc. as the outer layer of composite anti-corrosion. At the same time, phosphoric acid and phosphate compounds are used in a large amount in the phosphating process, which is prone to phosphorus pollution, causing adverse consequences such as eutrophication of water, and environmental contamination. Compared with the phosphating agent, passivating agent has simple components and does not contain phosphoric acid and phosphate compounds, and thus, it is more environmentally friendly.