What new directions can 5G bring to industrial intelligent manufacturing?
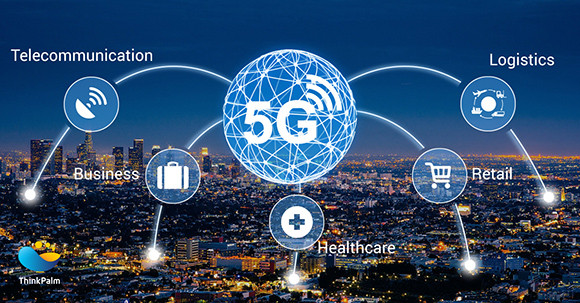
The development of 5G brings the realization of the Internet of Things and the convenient use of AR. When these technologies are applied to industry, the prototype of intelligent manufacturing can also be portrayed. So how does 5G technology apply to intelligent manufacturing in industry? What new directions can 5G bring to industrial intelligent manufacturing?
Specific standards for smart manufacturing
First, we need to understand the standards of smart manufacturing. The Ministry of Industry and Information Technology is now conducting the 2018 smart manufacturing pilot demonstration project recommendation work, and has clarified the elements and conditions of the 2018 smart manufacturing pilot demonstration project. Let us take a look.
1. A digital model has been established for the overall design, process flow and layout of the workshop / factory, and simulations have been performed to realize digital management of the entire process of planning, production and operation.
2. Apply digital 3D design and process technology for product, process design and simulation, and verify and optimize through physical testing and experiments. Establish a product data management system (PDM) to achieve integrated management of product design and process data.
3. The numerical control rate of manufacturing equipment exceeds 70%, and the information interconnection and integration between key technical equipment such as high-end CNC machine tools and industrial robots, intelligent sensing and control equipment, intelligent detection and assembly equipment, intelligent logistics and storage equipment, etc.
4. Establish a production process data collection and analysis system to achieve automatic upload of production site data such as production progress, field operation, quality inspection, equipment status, and material transfer, and to realize visual management.
5. Establish a workshop manufacturing execution system (MES) to achieve planning, scheduling, quality, equipment, production, energy efficiency and other management functions. Establish an enterprise resource planning system (ERP) to realize business management functions such as supply chain, logistics, and cost.
6. Establish the internal communication network structure of the factory, and realize the interconnection of information between the manufacturing process, such as design, process, manufacturing, inspection, and logistics, and the manufacturing process and manufacturing execution system (MES) and enterprise resource planning system (ERP).
7. It has an industrial information security management system and a technical protection system, and has information security guarantee capabilities such as network protection and emergency response. Built-in functional safety protection system, adopting full life cycle method to effectively avoid system failure.
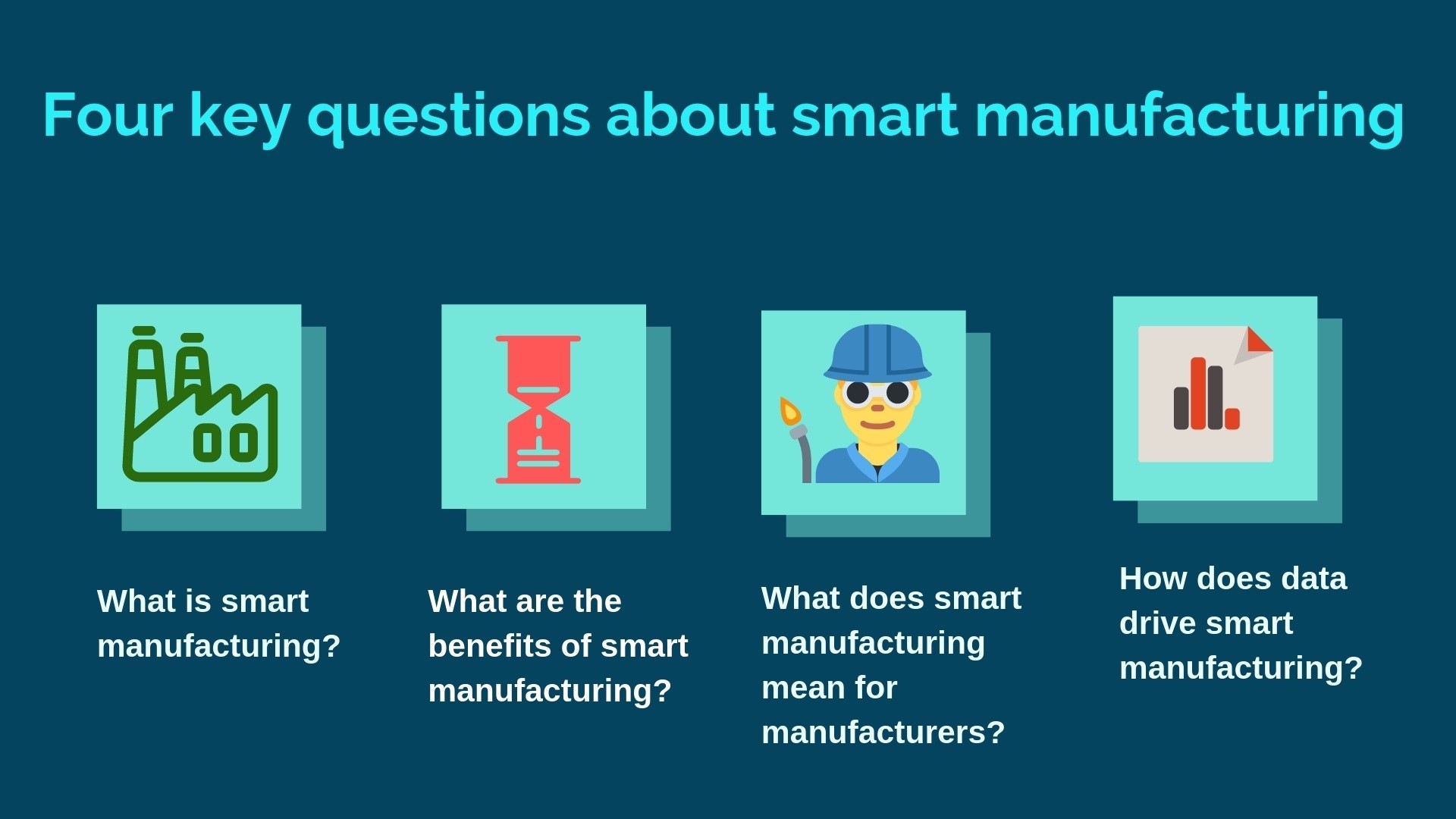
Key technologies brought by 5G
In terms of core networks, 5G should be said to have adopted the concepts of NFV (Network Function Virtualization) and SDN (Software-Defined Networking). Most of them are based on a software and hardware separation architecture. It seems that everyone is a server, and many different functional units are virtualized on it. From the perspective of network function design, the control and data plane are also better separated. Secondly, in terms of network architecture, it is further flattened. In the past, the four layers of 2G and 3G have become three layers to 4G, and 5G has become more concise and two layers, and many applications have mobile edge computing. Core network standards focus on implementations such as network slicing and mobile edge computing to ensure end-to-end user security.
In addition, the technical advantages of 5G technology are also reflected in millimeter waves, small base stations, large-scale antennas, and beamforming. Considering the advanced and economical aspects of 5G, 5G network construction is divided into two modes: non-independent networking and independent networking. The so-called independent networking is to use the new 5G air interface to access the new 5G core network. End-to-end is a complete 5G standard. The non-independent method is more reflected in the core network part, that is, some operating companies still use the 4G core network to access the new 5G interface as a transition in the initial stage to reduce initial investment.
In the process of promoting the implementation of the Internet of Things, eMBB can support high-bandwidth application scenarios such as remote video surveillance and video conferences; mMTC can meet the data connection and transmission requirements of a large number of low-power embedded terminals. URLLC can reduce the target of network latency to less than 1 millisecond to support many indicators and requirements for the real-time data transmission of systems and equipment in the process of industrial automation control.
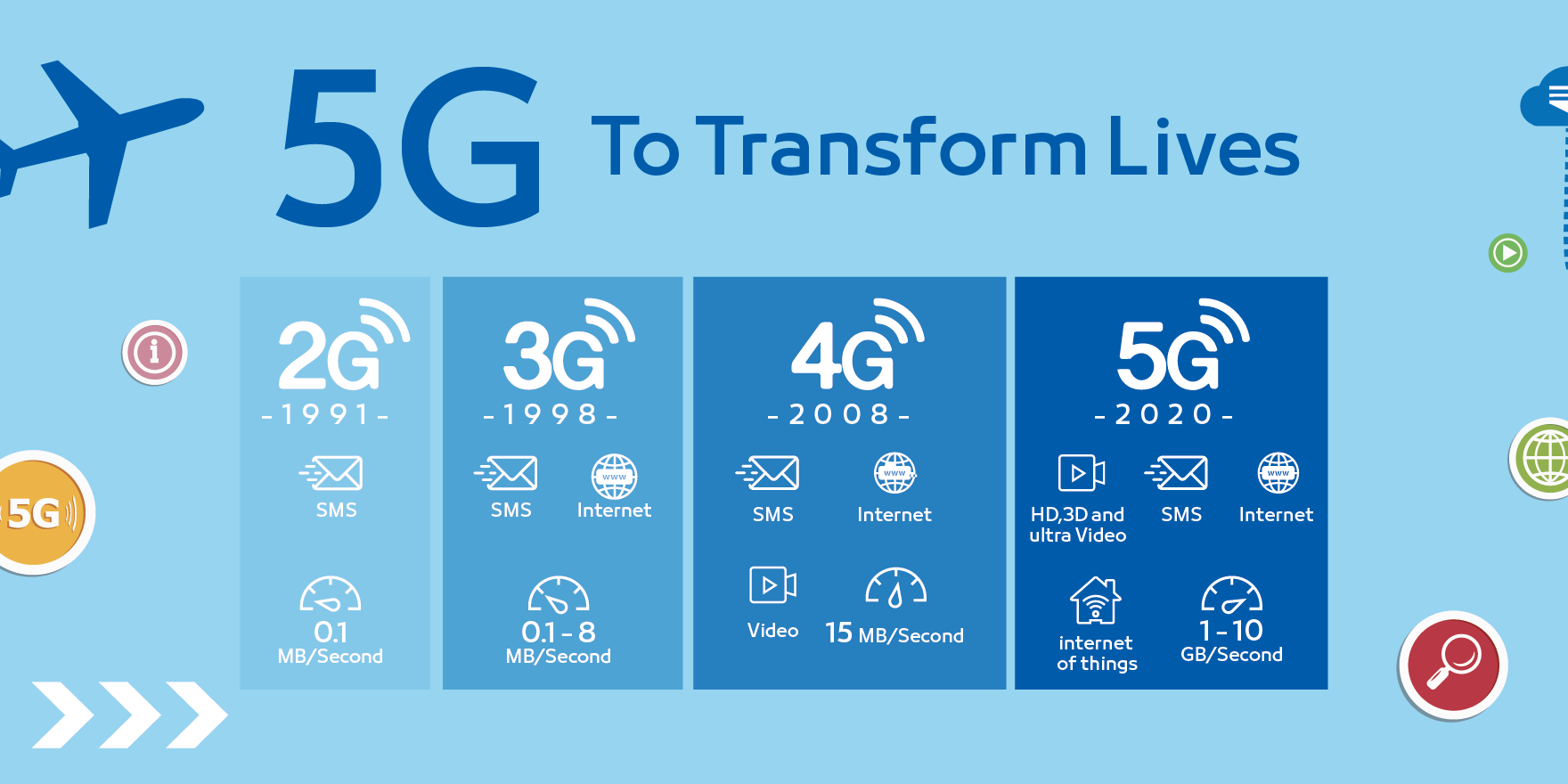
5G will support intelligent manufacturing in industry
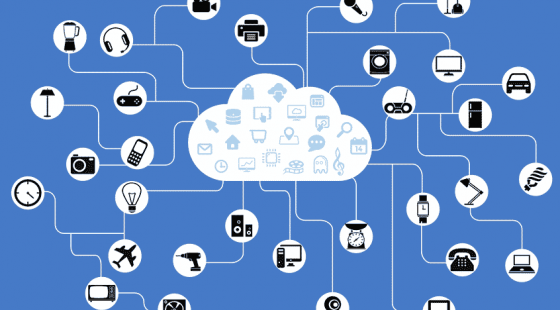
1. Internet Of Things
With the advancement of the intelligent transformation of factories, the Internet of Things, as a key supporting technology for connecting people, machines and equipment, is receiving great attention from enterprises. This demand, while promoting the application of the Internet of Things, has also greatly stimulated the development of 5G technology. In the face of complex industrial interconnection needs, 5G technology needs to adapt to different industrial scenarios, and can meet most of the Internet of Things' connection requirements. Therefore, 5G and the Internet of Things are complementary and complementary. The application of IoT depends on 5G to provide wireless connection solutions in different scenarios, and the maturity of 5G technology standards also needs the stimulation and promotion of IoT application requirements.
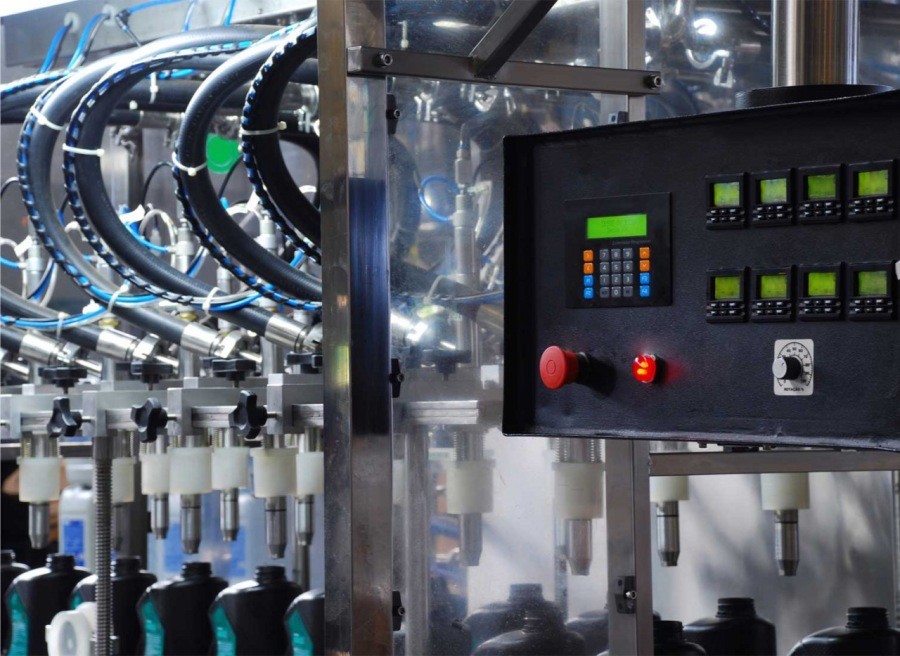
2. Industrial Automation Control
Automation control is the most basic application in a manufacturing plant, and the core is a closed-loop control system. Each sensor performs continuous measurement during the control cycle of the system, and the measurement data is transmitted to the controller to set the actuator. The typical closed-loop control process cycle is as low as ms level, so the system communication delay needs to reach ms level or even lower to ensure accurate control of the control system, and at the same time, it has extremely high requirements for reliability. If the delay in the production process is too long, or the control information is incorrect during data transmission, it may cause production downtime and cause huge financial losses. 5G can provide extremely low-time extension, high reliability, and massively connected networks, making it possible for closed-loop control applications to connect through wireless networks. Based on Huawei's 5G measured capability: the air interface delay can reach 0.4ms, the single cell downlink rate can reach 20Gbps, and the cell can support a maximum of 10 million + connections. It can be seen that only 5G networks in mobile communication networks can meet the requirements of closed-loop control on the network.

3. Logistics Tracking
In the already-scaled machine-to-machine market, its applications will include personnel tracking and high-priced products in transit. But (relatively) high connection costs limit growth in this market. 5G is expected to provide additional advantages in terms of deep coverage, low power consumption and low cost (economy of scale) and as a 3GPP standard technology. The improvements provided by 5G will include optimizing logistics in a wide range of industries, improving worker safety and increasing the efficiency of asset positioning and tracking, thereby minimizing costs. It will also expand capabilities to enable dynamic tracking of a wider range of goods in transit. As online shopping increases, asset tracking will become more important. In terms of logistics, from warehouse management to logistics distribution, wide-area, deep-coverage, low-power, large-connection, and low-cost connection technologies are required. In addition, the end-to-end integration of the virtual factory spans the entire life cycle of the product. To connect a wide range of sold goods, low-power, low-cost and wide-coverage networks are also required. Horizontal integration within or between companies The ubiquitous network is also needed, and 5G networks can meet this kind of demand very well.
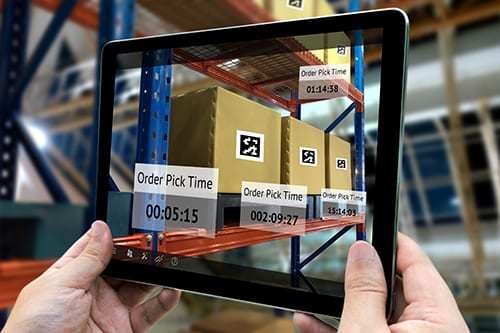
4. Industrial AR
In the future smart factory production process, people will play a more important role. However, due to the high degree of flexibility and versatility of future factories, this will place higher demands on factory floor staff. In order to quickly meet the needs of new tasks and production activities, augmented reality AR will play a key role in the intelligent manufacturing process and can be used in the following scenarios: such as monitoring processes and production processes. Step-by-step instructions for production tasks, such as manual assembly process guidance; remote expert business support, such as remote maintenance. In these applications, auxiliary AR facilities need to be as flexible and portable as possible in order for maintenance to be carried out efficiently. Therefore, it is necessary to move the device information processing function to the cloud. The AR device only has the function of connection and display. The AR device and the cloud are connected through a wireless network. AR equipment will obtain necessary information (for example, production environment data, production equipment data, and troubleshooting information) in real time through the network. In this scenario, the display content of the AR glasses must be synchronized with the movement of the camera in the AR device to avoid the step out of vision range. Generally, the response time from visual movement to AR images is less than 20ms, and there will be better synchronization. Therefore, the cloud backhaul required to transfer data from the camera to the cloud to AR display content needs to be less than 20mms. Delay, the two-way transmission delay of the wireless network must be within 10ms to meet the needs of real-time experience. However, the delay requirement cannot be met by the LTE network.
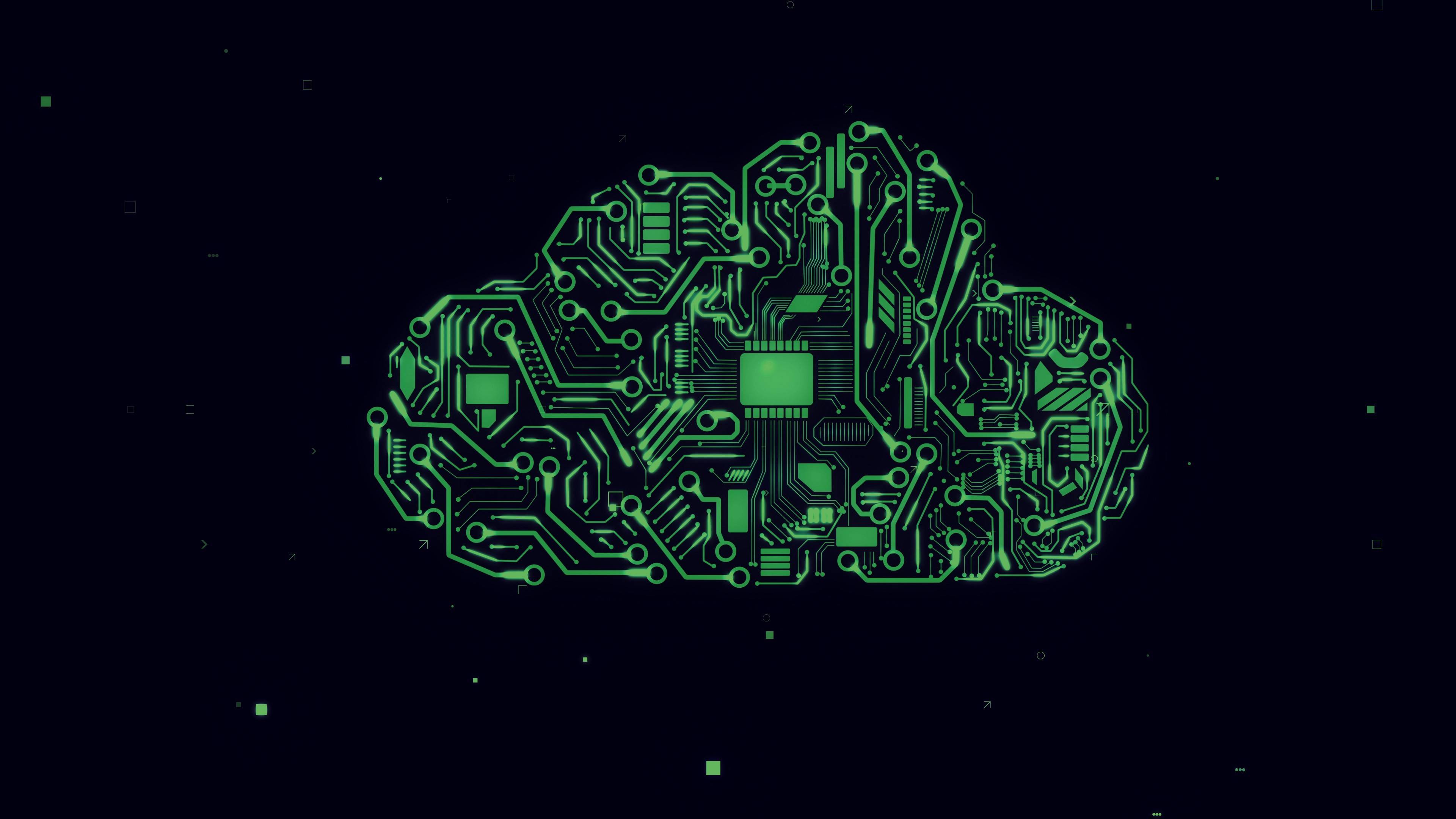
5. Cloudification Robot
In the intelligent manufacturing production scenario, robots are required to have the ability to self-organize and collaborate to meet flexible production, which brings the robot's demand for cloudification. Compared with traditional robots, cloud-based robots need to be connected to a cloud-based control center via a network, based on a platform with ultra-high computing power, and perform real-time operational control of the manufacturing process through big data and artificial intelligence. Through cloud technology robots, a large number of computing functions and data storage functions are moved to the cloud, which will greatly reduce the hardware cost and power consumption of the robot itself. And in order to meet the needs of flexible manufacturing, the robot needs to meet the requirements of free movement. Therefore, in the process of robot cloudification, wireless communication networks are required to have extremely low latency and high reliability. 5G network is an ideal communication network for cloudized robots, and it is the key to enable clouded robots. 5G slicing networks can provide end-to-end customized network support for cloud-based robot applications. 5G networks can achieve end-to-end communication delays as low as 1ms, and support 99.999% connection reliability. The strong network capability can greatly meet the challenges of delay and reliability of cloud-based robots.
5G technology will realize the integrated connection of products, employees and equipment. While standardizing corporate governance, it will also greatly improve the production efficiency of enterprises and promote the intelligent manufacturing of enterprises.