Home / All / Application of NdFeB / Application of magnetic consolidation pressure on the composite lay-up in the vacuum bag
Application of magnetic consolidation pressure on the composite lay-up in the vacuum bag
Improving laminate quality
The use of fiber reinforced polymer composites in a number of applications in energy, marine, aerospace, and automotive industries stem from their high specific stiffness and strength. However, there’s a major challenge to reduce manufacturing as well as tooling costs while minimizing structural defects, therefore, leading to a longer service life.
Wet lay-up's shortcomings in the past
Wet lay-up method has been implemented to fabricate fiber reinforced composites for strengthening of civil infrastructure, repair of aerospace structures, marine, and automotive industries. The extensive use of this method stems from minimal tooling cost, low cost of materials, and ease of application. However, there’s the shortcoming of emission of volatiles, which is a major concern of these open-mold processes. Low fiber volume fraction as well as high void content is another limitation associated with the wet lay-up method. These lead to products with low mechanical properties when compared to laminates fabricated by closed-mold methods.
Theory of the magnet assisted composite manufacture
Wet lay-up process in conjunction with vacuum bagging appears to be promising in the prevention of emission of volatiles and fabrication of better quality products if an elevated pressure can be applied to improve the consolidation. Researchers led by Professor M. Cengiz Altan at the University of Oklahoma developed the magnet assisted composite manufacturing method in a bid to improve the wet lay-up/vacuum bag process. The manufacturing approach does not necessitate complex tools for fabrication and may be implemented in the composite industries.
The actual operation as follows
They used six layers of E-glass, random fiber mats that were cut into squares as reinforcement. An epoxy resin (EPON 862) and a curing agent (EPICURE 3300) were mixed at room temperature. Then, the authors prepared the wet lay-up by applying one ply of dry fiber on the bottom steel tool plate and one coat of resin. They used a roller to squeeze the excess resin after laying each ply. The same procedure is repeated for all the plies. The composite was then covered with a caul plate, a porous release film, and a breather cloth and the entire lay-up is vacuum bagged. To apply the consolidation pressure, the authors used a set of Neodymium Iron Boron (NdFeB) permanent magnets that can generate a maximum magnetic pressure of 0.64 MPa. Nine magnets were placed on a magnetic steel plate and were used to produce a magnetic compressive pressure on top of the vacuum bag that was sandwiched between the magnets and bottom steel tool plate.
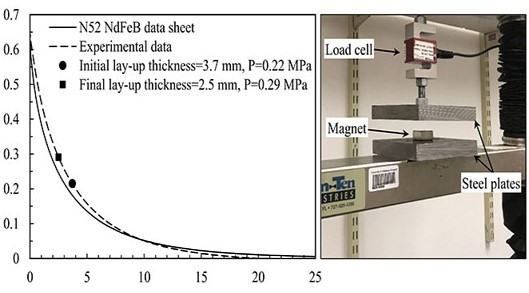
Variation of magnetic compressive pressure with air gap or lay-up thickness for an NdFeB, N52-2.54 × 2.54 × 1.27 cm3 magnet sandwiched between two steel plates.
In the study, the team fabricated 6-ply E-glass/epoxy laminates under four scenarios. In the first case, they fabricated the laminates by wet lay-up/vacuum bag method without applying an extra pressure. Therefore, the laminates were only compacted by the vacuum pressure. In the second case, M-T180 laminates were analyzed in order to understand the effectiveness of the magnet assisted composite manufacturing method and how it could enhance the typical wet lay-up/vacuum bag process. The third and fourth scenarios were considered for the assessment of the influence of applying magnetic consolidation pressure for a short period.
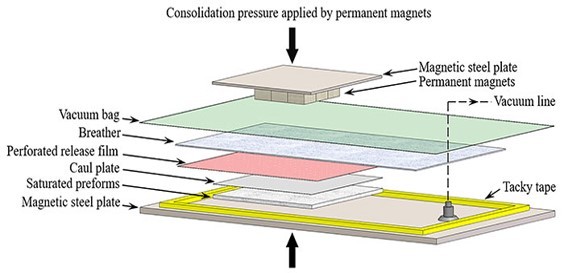
Application of magnetic pressure to consolidate the wet lay-up/vacuum bag composites.
Samples synthesized adopting magnet assisted composite manufacturing method exhibited approximately a 70% drop in the void volume fraction, 55% fiber volume fraction increase, and an improvement of the flexural strength as well as stiffness. Flexural strength increased by 60% to 253.5 MPa and the flexural stiffness was raised by 46% to 9.9 GPa. The authors also investigated the effect of time of applying magnetic pressure on the integrity of the products. They recorded the lowest void content when the magnetic pressure was only applied for 15 minutes while the fiber volume fraction was also increased by 22%.
Disclaimer: This post is for the free exchange of ideas and commentary regarding issues of interet to those in the field of magnetic or or other industries. If the post infringes your legal rights, please contact us with proof of ownership, we will delete it in time