Some introduction to powder metallurgy
1. What is powder metallurgy?
Powder metallurgy is a technology that manufactures metal powder, and uses metal powder (sometimes also adding a small
amount of non-metallic powder) as a raw material to produce materials or products through mixing, forming, and sintering.
It includes two parts.
(1) Manufacturing metal powder (also including alloy powder, hereinafter collectively referred to as "metal powder").
(2) Using metal powder (sometimes also adding a small amount of non-metallic powder) as a raw material, after mixing, forming
and sintering, manufacturing materials (called "powder metallurgy materials") or products (called "powder metallurgy products").
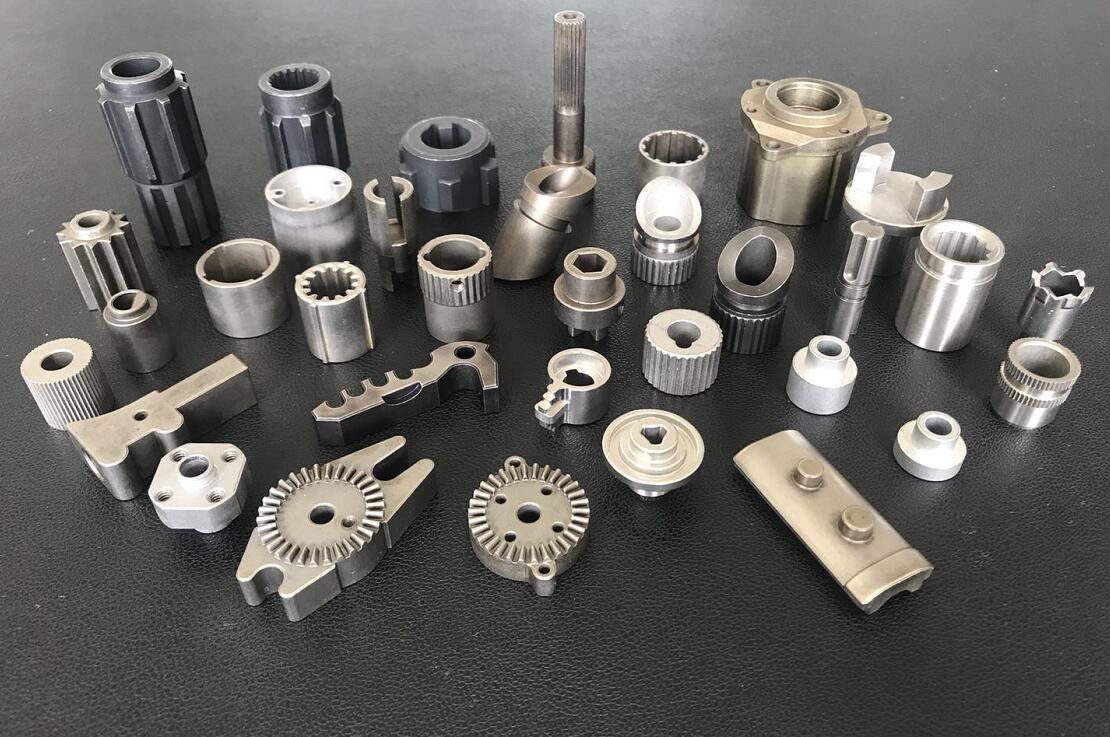
2. The prominent advantages of powder metallurgy.
(1) Able to manufacture materials and products that cannot be manufactured or are difficult to manufacture using other
processes,
such as porous, sweating, shock absorption, sound insulation and other materials and products, refractory metal materials and
products such as tungsten, molybdenum, titanium, metal-plastic, Bimetallic composite materials and products.
(2) It can directly manufacture products that meet or approach the size requirements of the finished product, thereby reducing or
eliminating mechanical processing. The material utilization rate can be as high as 95% or more. It can also replace copper with iron in
some products, which achieves "saving materials." , Energy saving ".
3. What is the particle size range of the powder?
Powder size range refers to the size of powder particles that vary between two specified sizes.
If the particle size range of a powder is -80 + 150 mesh, it means that the particle size of these powders is equal to or less
than 80 mesh and greater than 150 mesh. In other words, these powders passed the 80 mesh sieve, but not the 150 mesh sieve.
4. What are the special powder forming methods?
(1) Isostatic pressing; (2) Continuous forming; (3) Pressureless forming; (4) High energy forming; (5) Injection forming.